How to replace foam and plastic packaging with mushroom experiments
On this week's "TechKnow," expert contributor Lindsay Moran travels to Green Island, N.Y., to investigate how mushrooms are being used to create eco-friendly packaging and insulation materials.
"We're taking local farm waste and mixing it with tissues from mushrooms and growing replacements for plastic foams that are used in protective packaging," explains Gavin McIntyre, co-founder and one of the chief scientists at Ecovative Design, a "revolutionary new biomaterials company" in Green Island.
"It's not like plastics equals bad," explains McIntyre's business partner, Eben Bayer. "It's that they're fundamentally incompatible with the earth's biosphere."
More traditional Styrofoam packaging is made of polystyrene, an unsustainable petrochemical, and can take up to a million years to biodegrade naturally. One of Ecovative's goals is to develop packaging materials that not only decompose faster and more naturally, but also give back to the ecosystem. They do this by utilizing mycelium, the microscopic root structure that allows mushrooms to grow on trees and spread throughout the forest floor.
"The initial concept of using mushroom roots, or mycelium, as a resin was inspired when I saw mycelium growing through woodchips and holding them together," Bayer says. The final concept came together when he paired up with McIntyre, and together they developed Ecovative's revolutionary production process.

Local agricultural waste, such as corn stalks and husks, is cleaned and then mixed with mycelium. The mixture is incubated for about two days before being ground up and packed into molds. After allowing the mycelium to grow and fill out for about three more days, the molds are baked in a low-temperature oven to prevent further growth. They are then removed from the molds and trimmed to fit as packaging pieces for electronics, car parts, and more.
"We actually never grow mushrooms," Bayer explains. "We just keep the mycelium in this vegetative growth stage where it's always making more of this root structure."
Ecovative's packaging biodegrades much quicker than traditional polystyrene--a piece of their packaging can decompose in just a few months. It also adds helpful nutrients back into the soil.
But Ecovative doesn't draw the line at sustainable packaging. They're currently developing insulation for houses, using the same mushroom root growth structure to create a layer between the interior walls and exterior siding. The mycelium growth between the walls provides insulation, structure, and even an extra layer of protection for homes.
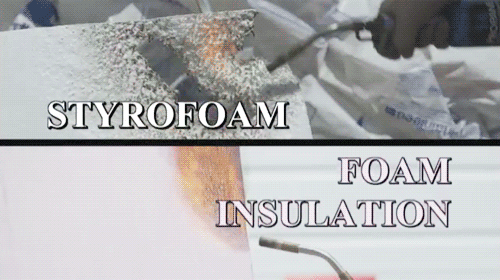

"The mycelium itself acts as a sort of fire retardant," one of Ecovative's employees explains to Moran, comparing Ecovative's insulation to quick-igniting traditional foam insulation. "We can keep an open flame on this for a few minutes before it actually becomes any danger. Overall, you're going to have more time to get out of your house."
"We see this as looking forward centuries, not just days," McIntyre concludes. "We want to make sure that this environment is available for our grandchildren and our grandchildren's children and that we're taking the best use of the natural resources that are provided to us today."
Watch "TechKnow," Sundays at 7:30PM ET/4:30PM PT on Al Jazeera America.
Error
Sorry, your comment was not saved due to a technical problem. Please try again later or using a different browser.